10 Supply Chain Metrics That You Should Be Monitoring
How can you find out how your business is doing?
You wouldn’t typically rely on your gut feeling or how you feel things are going. Instead, you’d track critical data points and crunch numbers to evaluate your company’s performance.
The same approach should be used to evaluate your supply chain. Supply chain metrics are a great way to get a clear picture of the performance of your supply chain. These metrics are like rulers that allow you to measure the quality, efficiency, success, and overall performance of your supply chain.
This article will discuss five key supply chain metrics you should track and tips to improve your supply chain metrics over time.
What are supply chain metrics?
Supply chain metrics, also known as supply chain key performance indicators or KPIs, are numbers, ratios, and parameters that can be used to measure supply-chain performance.
Supply chain metrics measure different aspects of your supply chains, such as delivery and inventory movements, to give insight into their efficiency and quality.
What is the importance of supply chain metrics?
Metrics of the supply chain are crucial for measuring progress toward a company’s goals. They give visibility into essential functions and ensure that all parts of the supply chain are monitored and run smoothly.
Therefore, a company can track its supply chain metrics to identify areas that need improvement or improve supply chain efficiency. Businesses can become more proactive in dealing with challenges and increase the resilience and agility of their supply chains by having a better understanding.
A strong supply chain is crucial to thriving in today’s highly competitive business environment. It will also help you increase your revenue. Deloitte’s survey found that 79% of high-performing supply chain companies achieve higher revenue growth than the average for their industry. Monitoring your supply chain metrics (or “KPIs”) can help determine whether your supply chain performance has been satisfactory. These are parameters that quantify and define the performance of your supply chains. You need to monitor these top 10 performance indicators to optimize your supply chain management.
- Inventory Turnover
Inventory turnover is the amount of inventory sold within a given period.
A high turnover means that your products are selling quickly and that you have a high demand. Your inventory turnover rate may be lower than industry standards. It could indicate that you are overstocking. Proper forecasting and inventory automation software are crucial to improving your inventory turnover.
- Accuracy of Inventory
This metric compares your physical inventory to what is in your database. Inventory accuracy can reduce stock outages and inventory carrying costs.
This formula can be used to calculate inventory accuracy:
Database Inventory Count / Physical Inventory Count
You want to achieve an inventory accuracy rate between 95% and 99%. You can improve inventory accuracy by implementing good inventory naming practices and labeling. Warehouse management and inventory management software can be used to reduce manual data entry and human error.
- Order Fill Rate
The order fill rate refers to the number of orders a company can immediately ship from its stock. The order fill rate measures how efficiently your delivery service and customer demand are. This formula calculates the supply chain’s fill rate.
Total number of customer orders shipped / total number of customer orders filled x 100
A Tompkins Supply Chain Consortium report shows that leaders in fill rates are above 98%, and the average hovers around 95%.
Low order fill rates can be improved by proper demand forecasting, setting inventory replenishment parameters that prevent out-of-stock issues, and offering alternatives to out-of-stock items.
- Excellent Order Rate
The perfect order rate is the number of orders you ship with no errors or deviations. This metric allows you to track and manage your delivery and storage operations and gauge customer satisfaction.
A perfect order is based on four factors: delivery must be complete, on time, undamaged, and with the proper documentation.
The American Productivity and Quality Center data show that organizations have an average perfect order index of 90 percent. You can improve your order performance by taking orders accurately, allocating inventory quickly, delivering products on time, and sending accurate invoices.
- Shipment on-Time
On-Time shipping is the percentage of orders shipped before or on the date requested. This metric allows you to track your delivery performance and is crucial for customer satisfaction.
It can be measured using the following:
(Number Of On-Time Items/Total Items) x 100
High on-time shipping rates indicate a well-organized supply chain. Poor on-time shipping rates can mean that orders are not delivered on time. To avoid losing customers, it is essential to resolve issues quickly with on-time shipping.
- Backorder
Backorders are orders that cannot be fulfilled when a customer places them. This formula can be used to calculate the backorder rate.
Several undeliverable Orders/by the Total Number of Orders x 100.
If you have a consistently high number of backorders and long wait times, it could be a sign that something is not correct. An inventory system can help reduce backorders. It provides real-time information about your stock levels, allowing you to reorder products before stock runs out.
- Time to Order
The order cycle time (also known as inventory cycle length) is the average time a customer’s product arrives after they place an order. This metric uses the following formula:
Actual Ship Date – Customer order Date
Customers who have short order cycles are more likely to be responsive. Long order cycles can indicate that your operations are not in sync. Review all the steps involved in picking and shipping orders to save time.
- Inventory Days
Inventory days on hand is the average time it takes for inventory to be sold. This metric allows you to know when it is time to replenish your stock.
This formula can be used to calculate inventory days per hand:
(Average inventory for the year / Cost of goods sold) x 365
Your inventory days on hand rate may be high if it needs to be managed appropriately or has complex sell inventory.
- Rate of Return
The rate of return metric is the rate at which your shipped items are returned.
The formula below can be used to calculate this metric:
Total Items Returned / Total Items Shipped
It would be best to discover why customers return orders to gain insight into your return rate. It will allow you to spot weaknesses in your supply chain and make the necessary improvements.
- Select Accuracy
You can accurately pick orders by determining the accuracy of order picking. Incorrect picks can lead to inaccurate inventory, delayed shipping, and unhappy customers. This formula can be used to calculate the accuracy of order picking:
Total Orders / Perfect Rate
The 2019 DC Measures benchmarking study conducted by the Warehousing Education and Research Council (WERC) found that the best-in-class operations have more than 99.89% accuracy in order picking accuracy.
Pick items based on their item codes to increase accuracy, and automation is encouraged. You can group them together to make it easier to find similar items and reduce picking time.
Related Articles
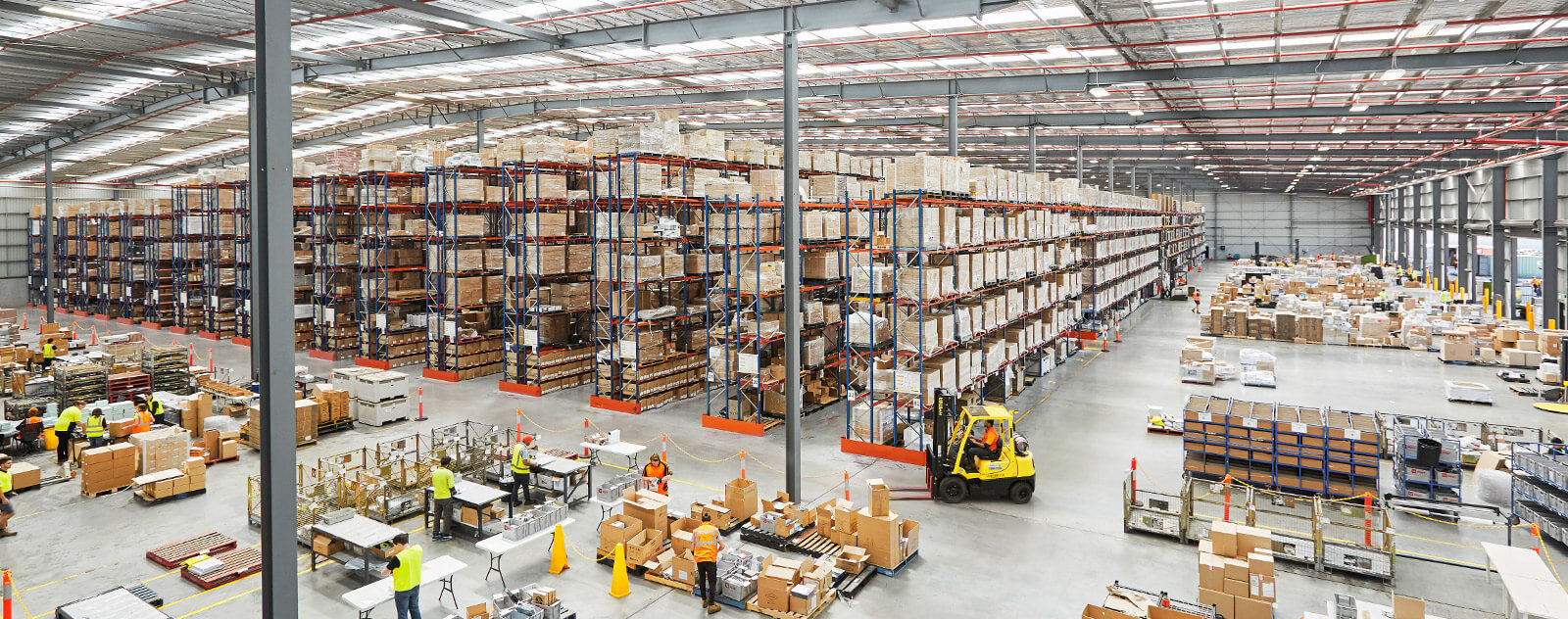
Why Should You Change Your Current 3PL Service Provider? When Is The Right Time to Change?
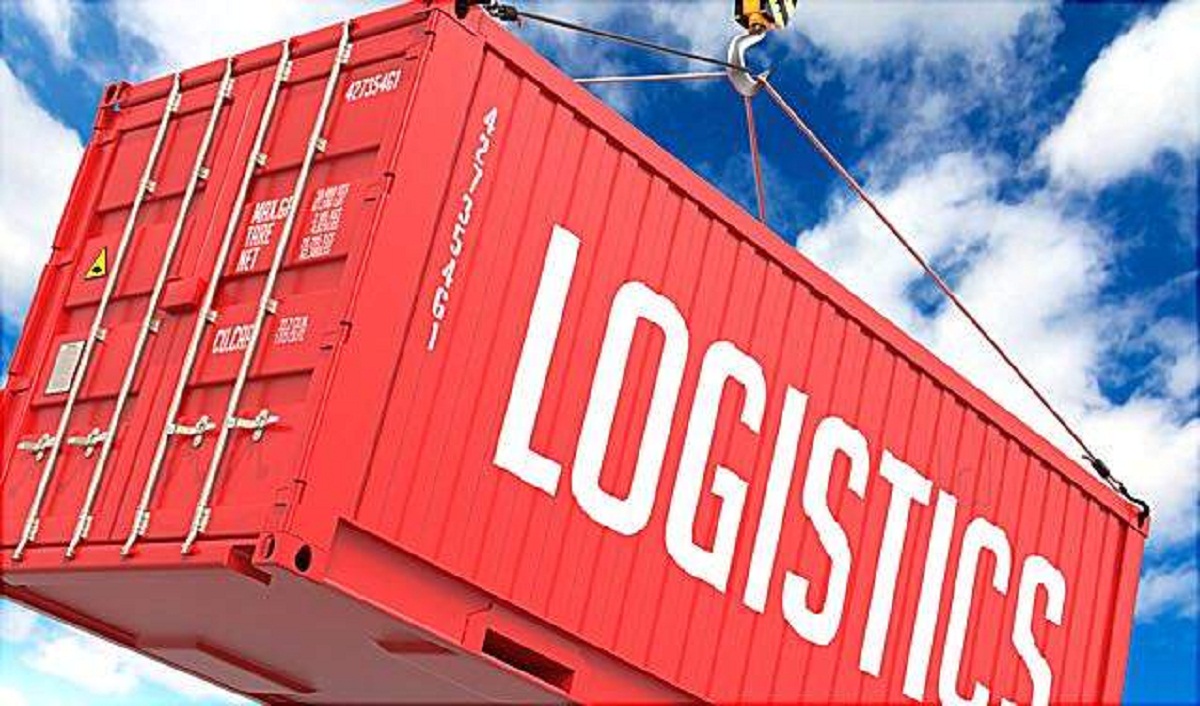
The Role of Logistics Management in The Retail Industry